If you are going to do any amount of gunsmithing—cleaning, bore sighting, stock work, or other types of job—you will want some device that holds the rifle or shotgun in a handy position. A gun vise is the best tool for this job, and there are several commercially available ones on the market, including the Decker Gun Vise, The Gun Cradle from Brownells, and the MTM Portable Maintenance Center. But if none of these suit your needs, or you simply don’t have the scratch to buy one, you can make your own vise with a few common tools.
There are two different approaches to the gun vise project, one very simple, and another that is more involved. The simpler gun vise is designed to hold the firearm’s receiver, while the more involved one holds the butt and the forearm rests on a V-shaped pad in front. I prefer the style that holds the butt and rests the fore-end, but only you can make the decision of how much effort should be expended on this project.
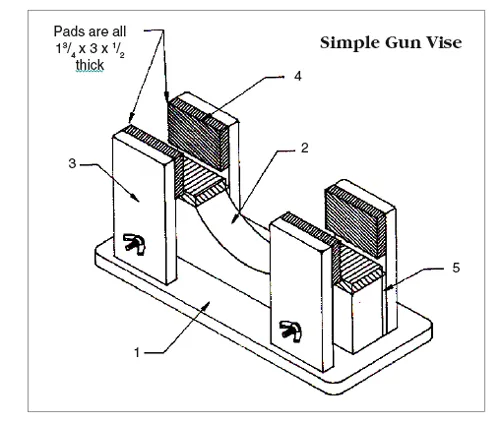
All Drawings Courtesy
You can purchase all of the materials for either job at a well-stocked hardware store in almost any city or township. I get most of the materials from the cut-off bins in handyman stores, since the pieces are already small and their sizes can be easily modified. The common woods found in handyman stores for around-the-house work are pine or fir, either is suitable for this project. If you can find priced cheaply, harder woods such as ash, oak, or the most practical, maple, are even better. Don’t plan on using particleboard. It just won’t hold up to this use.
The same home handyman store can supply the hardware you need: all-thread rod, carriage bolts, rubber appliance feet, wing nuts, washers, particleboard screws, and self-adhesive weatherstripping. The 1/4-20 wing nuts, 1/4-inch flat washers, No. 8 by 11/2-inch-long particleboard screws (flathead screws), the 5/16-inch-diameter by 3/4-inch-long rollpin, and 1/4-20 all-thread rod. Rubber or neoprene appliance feet are also sold as rubber bumpers, and just about any four alike will suffice. A good substitute for the feet would be four squares of tough neoprene foam glued on with a contact cement. Those of you who have used particleboard screws already know they are far superior to both woodscrews and drywall or sheetrock screws. Particleboard screws are stronger, easier to drive in, less prone to stripping the wood out, and the head sinks in better than other screws. Also, if you choose to use it, leather padding is more aesthetically pleasing than using weatherstripping for padding.
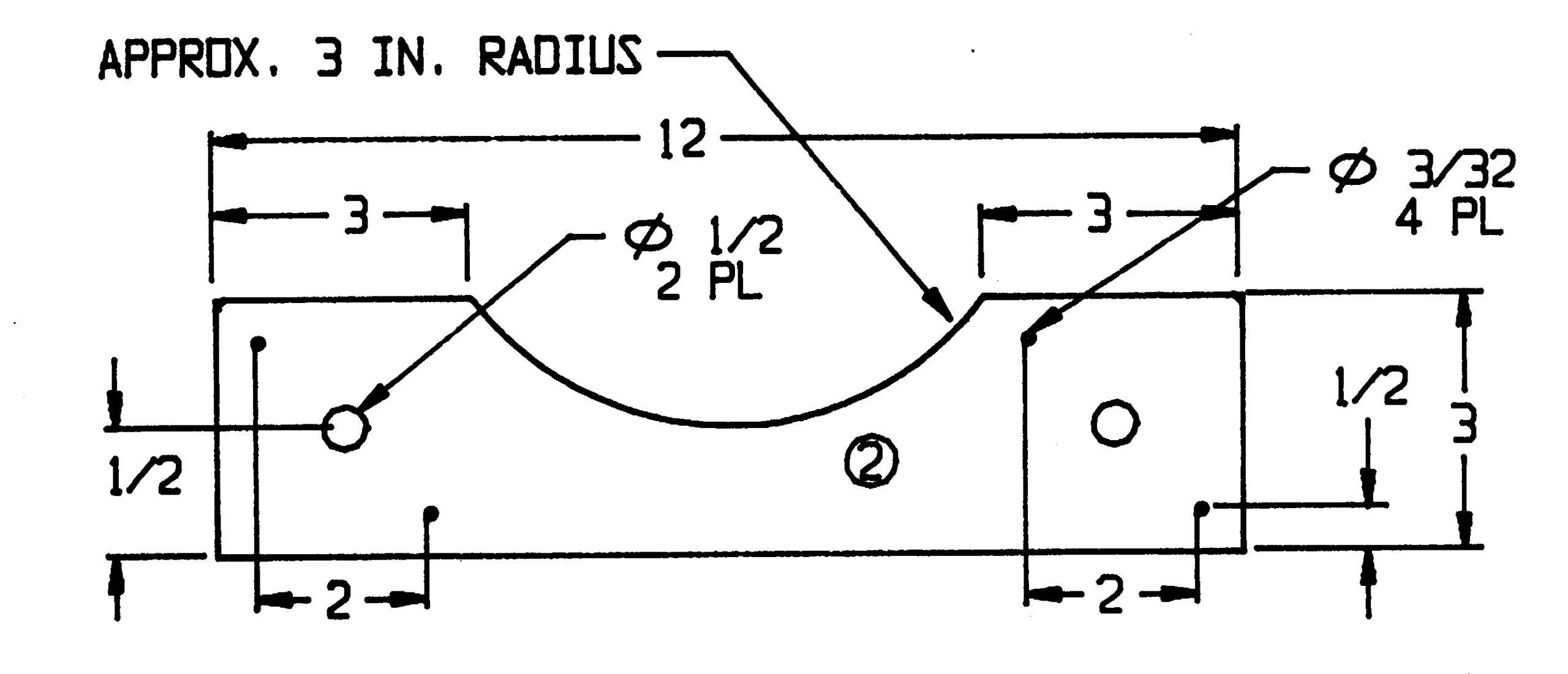
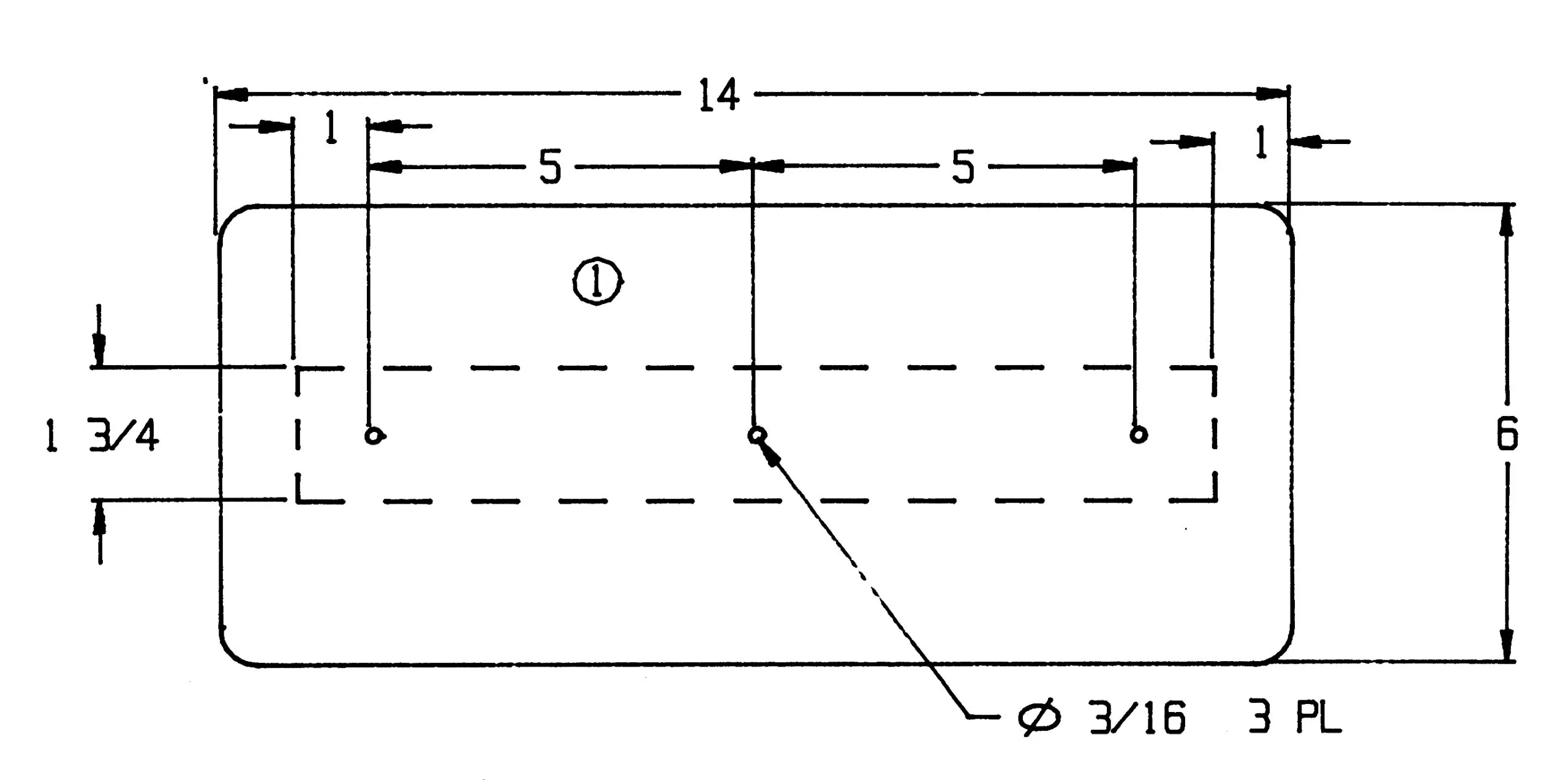
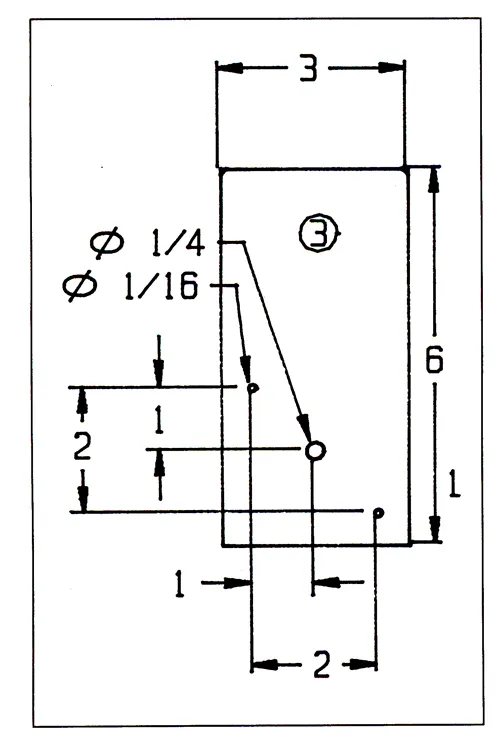
American Gunsmith
Either of these designs can be built in an afternoon, but the simpler one will take a reasonably adept woodworker less than an hour to make. If you plan on using the vise for a while, don’t rush it. Also, allow your mind to imagine the vise’s use as you are making it. You might think of other things you would want on the rig that aren’t included here. For instance, I added a small tray to the base of my gun vise to hold parts for jobs.
Building The Simple Vise
Measure and mark all the shapes of the eight pieces of wood you will use for this vise. There will be the four uprights of “one by” thickness, which measures out to be 0.588 inches thick. Other dimensions are detailed in Figure 1S. The plywood base could be made of the same material as the other parts, but I would want mine made out of plywood. Its shape is detailed in Figure 2S. The spine’s dimensions are detailed in Figure 3S.
The 1 3/4-inch-thick spine on the simple vise is made of three pieces of 0.588-inch-thick wood laminated together to achieve an approximation of that thickness. This measurement is not critical to the function of the vise and may be varied as you choose. There will, most likely, be some fitting required due to the varying thicknesses of the lumber available in different locations. The spine can be cut more quickly if you have access to a bandsaw or a sabre saw. It is not really necessary to have the cut relief curved, except to have clearance to remove some guns’ magazines, and it’s more pleasing to the eyes. The spine only connects the two active sections of the vise for rigidity. It will not be practical to install long magazines when a gun’s receiver is clamped in this vise.
To make the fit tighter and to minimize any rocking motion of the two floating uprights, the ones nearest you in the isometric drawing, leave the holes to be drilled after the other parts have been assembled. I will go into that drilling when we have glued all of the parts together that form the main vise assembly.
After cutting the pieces to match the diagram dimensions, sand them to whatever degree of smoothness your patience will allow and deburr around the drilled holes. I use a jitterbug sander with 100-grit white sandpaper followed by 320-grit white paper for this job.
Assemble the base, spine, the two quarter-inch spacers, and two of the uprights with ample carpenter’s glue between the contacting surfaces. I would start with the spine (2) and the base (1) and secure them together with three 2-inch-long No. 8 flathead woodscrews or particleboard screws.
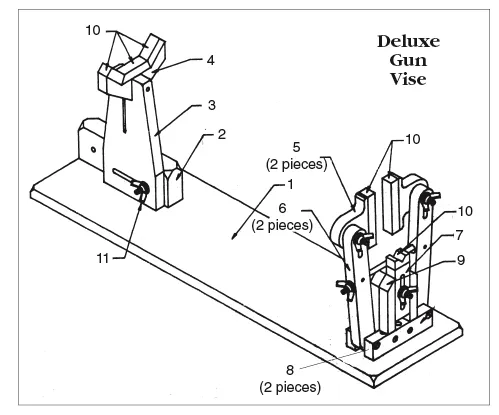
Add the two quarter-inch plywood spacers (5) and two uprights (3) to the base and spine assembly using plenty of the glue, and wipe up excess glue with a wet shop rag. Follow this with a dry rag to minimize the fuzzing caused by the water.
Clamp the two remaining upright pieces, (3), into position with the butts of the uprights firmly against the baseplate and the sides lined up with the ends of the spine, (2). Drill quarter-inch holes through the stationary uprights, and the spine and the holes will be lined up with the floating uprights in a steadier stance when they are moved in and out. The six-inch carriage bolts may be put through the spine from the glued upright side; then check the floating uprights for smooth movement. If they bind anywhere, carefully sand a small amount off of their bottoms to free them. Then, take the carriage bolts out until you finish the vise.
When the glue has dried clear, (usually after about an hour to be safe), you can paint or finish the main assembly and the two loose uprights. I would suggest using a urethane varnish or other paint that resists most of the solvents you will be using on guns. It should also be a gloss finish so that it can be kept clean more easily. If you used some pretty wood, you might want to use a clear urethane to show off your choice. Otherwise, I would use an opaque color to hide your practicality.
When the finish has dried, (usually overnight), contact cement the six neoprene pads, (4), at the proper locations shown in the drawing. The carriage bolts may now be glued in to prevent them from coming unseated so easily. To keep from getting glue into the threads of the carriage bolts, stick at least three inches of the threaded end into the stationary upright before adding glue to its shank. Add the floating uprights, flat washers, and wing nuts, and tighten the clamps to let the glue dry around the carriage bolts. If you already have one of the “Acra” products, such as Acra-Weld, Acra-Glas, or Acra-Gel, or J-B Weld, I would use them instead of glue around the carriage bolts.
Adding some soft leather over the pads gives a refined look, much like what I have with my “Gun-Mate” cleaning vise. I have noticed the interest of my customers when they see the vise, and it has helped break the ice when they mention the quality of it. A nicely made wooden one should bring the same results. Any little touch that gives your customer the feeling that you have good equipment, even if it’s a meaningless cosmetic touch, is worthwhile.
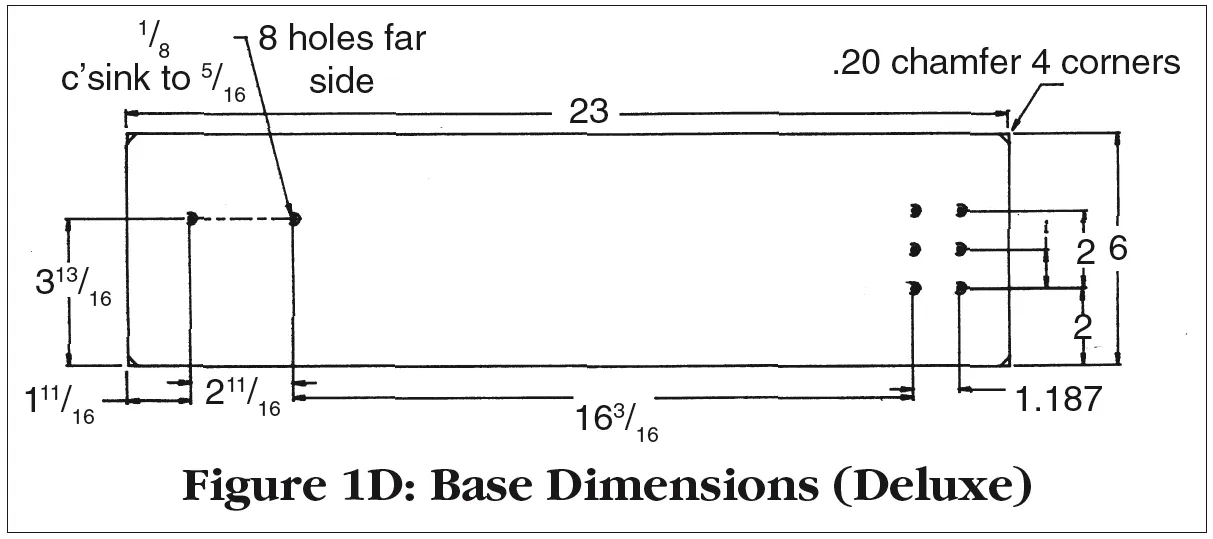
Building The Deluxe Vise
The deluxe gun vise takes more effort to build, and it holds the long gun in a different way, as you can see in the accompanying diagram. There are some angles and more curves to sand, but the overall benefits of this vise warrant the extra work. The pieces of the completed vise include: (1) base; (2) base/fore-end adjusting block; (3) the vertical fore-end support; (4) the fore-end rest; (5) stock pad arms; (6) the two vertical arms; (7) the butt riser; (8) the two supports; (9) the butt riser support assembly; (10) pad.
I would plan ahead and try to drill holes in places that will eliminate having to grind, file, or otherwise force smooth curves into places without the proper tools. Drill holes and saw into them at a tangent to obtain the radii needed.
All of the materials can be picked up at the local handyman store, and only you can decide how good a wood you might want to use. I would, however, make sure that the wood I used was hard enough to last a while. Search through the cut-off bins and get some hard, solid-core plywood for the base (1), and some hardwood like maple or oak for the other pieces. The drawing will show how large the pieces are to be, and you will want to give yourself some leeway for cuts that must run straight.
Laying the parts out on the wood with a pencil will probably turn out to be more work and bother than the actual cutting of the pieces. I would start out cutting the more difficult pieces to be able to finish the last pieces with your mind already planning the assembly. A bandsaw is a desirable tool for making the deluxe vise, but it’s not essential. The base dimensions are shown in Figure 1D; dimensions for the base/fore-end adjusting block in Figure 2D; the vertical fore-end support dimensions in Figure 3D; the fore-end rest measurements in Figure 4D; the two clamps in Figure 5D; the vertical arms in Figure 6D; the butt riser in Figure 7D; the two supports in Figure 8D; and the butt riser support assembly in Figure 9D.
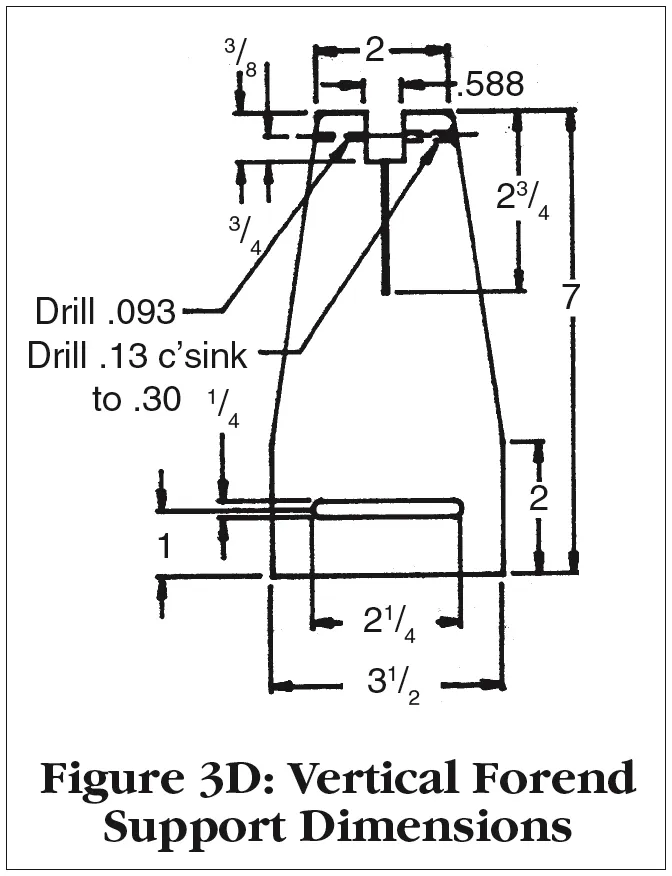
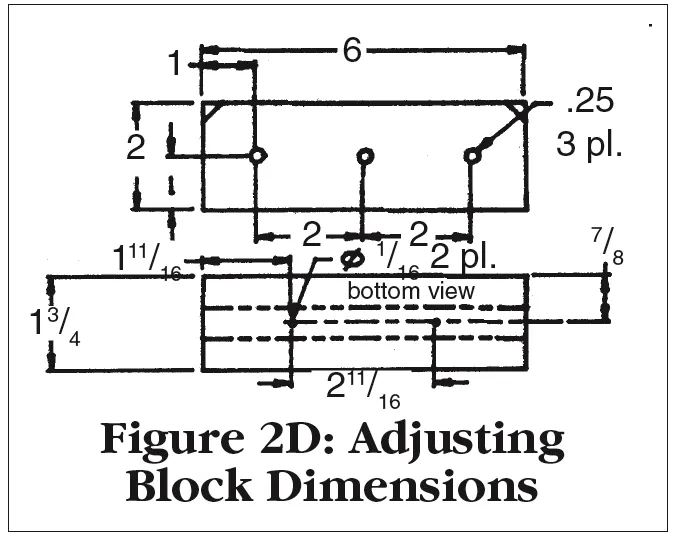
There are two places where the fit of mating pieces is important: the fore-end rest (4) to the vertical fore-end support (3); and the butt riser (7) to the butt riser support assembly (9). Piece 9 is an assembly of three pieces of wood, but is simple enough to be easily shown together in my drawing. It would be a good idea to leave a little bit of extra wood on the outside edges of the three parts of Piece 9 to allow for adjusting the fit between numbers 9 and 7.
I would mark the centerline of the main, 2-inch-wide piece of Piece 9 so that the side pieces can more easily be positioned when glueing them. A quick study of the drawing should indicate why these pieces must be fitted together just so if the vise is to be sturdy.
The slots in Pieces 9, 7, 6, and 3 are most easily made with a milling machine, but can be readily made with a router table.
If all of the pieces are sanded before being attached together, finishing sanding will be much easier, and I would certainly sand Pieces 1 through 6 before doing any glueing. Of particular interest should be the base (1), since it has the most surface and will be noticed more often.
After sanding until your fingers are at their limit, it is time to glue the pieces together, which will form a sturdy base assembly. Use a couple of 1/4-inch bolts or 1/4-inch steel pins to align pieces seven and nine before glueing the side pieces of wood to the two inch wide number nine. After the two side pieces are glued and clamped, remove Piece 7 and clean up all excess glue from both pieces.
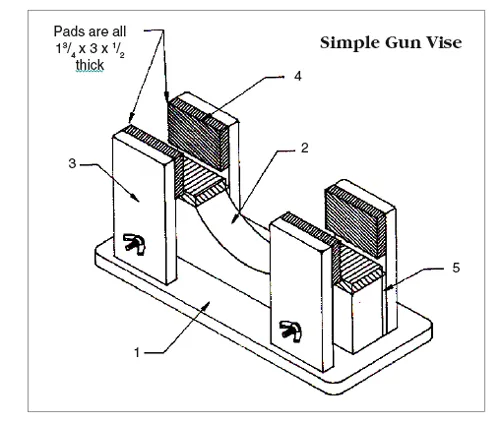
All Drawings Courtesy
0)]
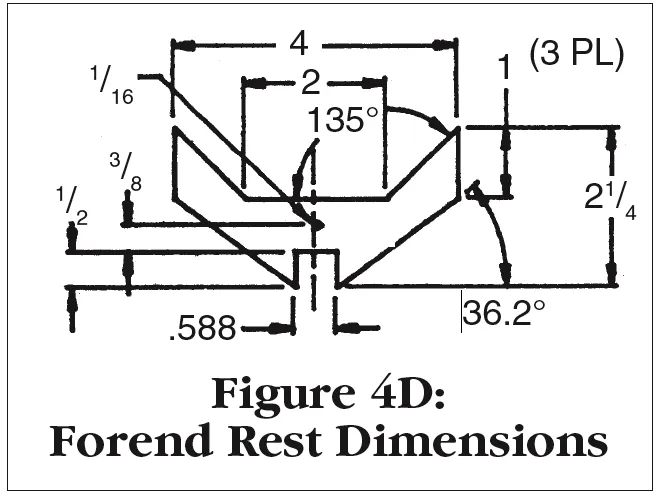
Pieces 3 and 4 should have glue applied to their mating notches and surfaces, and the screw installed to clamp them together. This is the purpose for that curious saw-cut on Piece 3. Spread glue on the base (1) and screw on Piece 2 with two flathead screws.
I suggest glueing the base (1), the two supports (8), and the assembly (9) together in a continuous operation. They all need to be pulled together with the screws while the glue will still slip. If the screw holes were marked and drilled fairly accurately, the whole lower base should keep everything in line when the complete vise is assembled.
I believe in assembling the parts before finishing them to see how they fit. It helps to wash your hands before handling the hardware along with the unpainted wood, so that you will not soil the wood and spoil the professional look you are striving for. It is not unusual to have to sand in more clearance between parts, because lumber isn’t as consistent in thickness as it would be if it were run through a thickness planer.
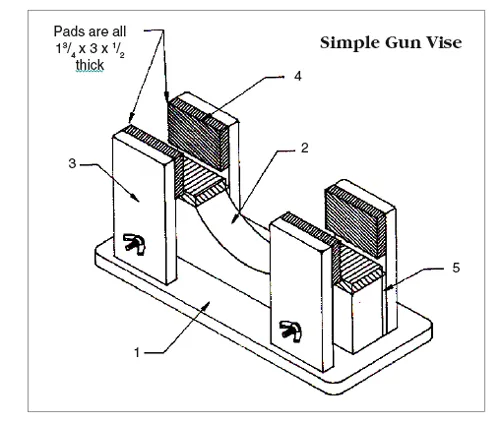
All Drawings Courtesy
2)]
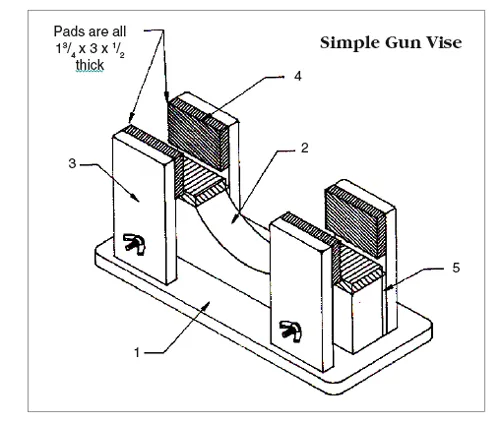
All Drawings Courtesy
1)]
If you’re unable to find an appropriate hanger bolt (see Piece 12 in Figure 8D), you can make one. Just get a 7-inch length of 1/4-20 “all-thread” rod from the hardware store, and mash one end with a bench vise or a hammer. When you’ve mashed it down to about 1/8 inch in thickness, file or grind the widened end, smooth, and drill a 11/64-inch hole in it. It is only necessary to have the hole large enough to allow free rotation of the 5/32-inch rollpin used to anchor it to one of the two vertical arms (6).
The final sanding should be done with white, 100-grit stearite sandpaper followed with a good sanding with 320-grit paper. All edges that might come in contact with a gun you have to work on should be blended so that there are no edges sharp enough to dent the gun’s wood. When the surfaces are also smooth enough, dust the entire vise off and wipe it with a clean rag before applying the finish.
As mentioned earlier, I use urethane finishes on the things I feel need a hard surface that resists most solvents used in the gun business. It doesn’t matter whether you use spray-can varnish or brush it on, just use plenty so there will be a continuous finish without any grainy roughness or pores to catch dirt or other foreign substances. Wood will usually fuzz up after the first coat, so plan on letting the first coat dry very well and either lightly sanding it to remove the fuzz or use a XXXX steel wool or Scotchbrite pads. Some soft wood might require a second de-fuzzing, but a second coat of the urethane varnish should fill in the pores.
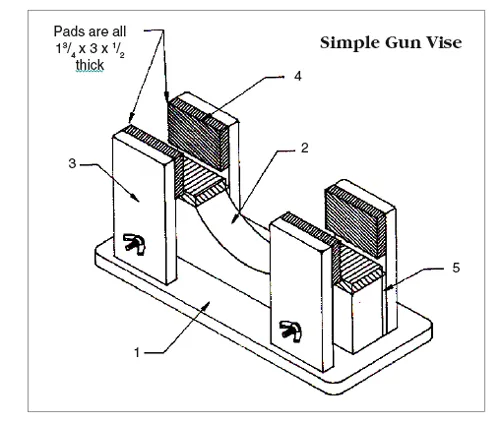
All Drawings Courtesy
4)]
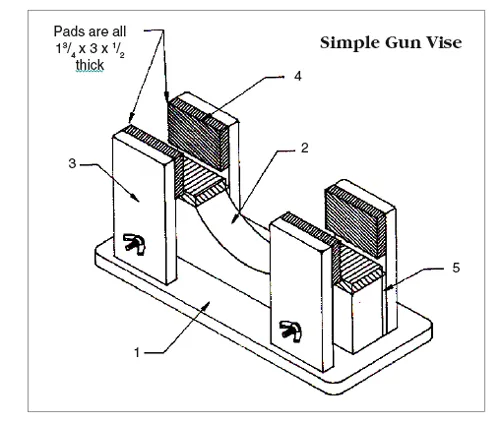
All Drawings Courtesy
3)]
Let the parts dry for a respectable amount of time, usually 24 hours after the last coat is applied, assemble the parts having a flat washer between each wingnut and the wood, and the rubber feet screwed onto the bottom of the base. The 5/32-inch rollpin will need to be driven through the arm and the hanger bolt before installing the two arms onto the base assembly.
The 1/2-inch-square weatherstripping should be cut to fit before removing the backing, as it may need to be trimmed several times before getting the right fit. I ground some of the ends on my disk sander by touching it lightly to the disk so it wouldn’t distort. Put these pieces (10) aside until the very last step.
When fully assembled, the vise only needs to have the foam pads stuck into place and mashed firmly to seat the adhesive backing into the wood’s pores. If you recently used any contact cement on the pads, it should be allowed to dry overnight before you set a gun’s finish near it. The vise is now ready to try now. Think about screwing an eye screw into the side of the base to give you a way to hand it out of the way.
Im interested in making your deluxe vise but in the instructions there is no figure 5d,6d,7d,8d or 9d.
Please can you send me the complete instructions with all measurements for the pieces I need to cut so I can put it all together.
Thanks, Paul
if there are plans for sale I would gladly buy them.
Yeah, what Paul Lee said back in Dec. 2021
(FS)